Drill Machine - The Different Types of Drills & The Benefits They Have
Published On: Feb 01, 2022 by Pathak
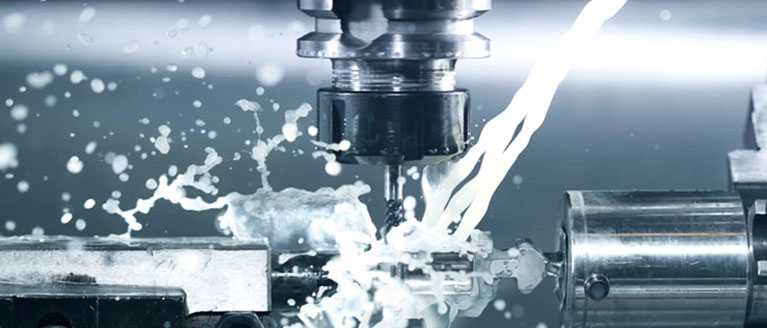
These machines are often used for tapping of metal and wooden surfaces. They're a must-have for any industry that requires metal tapping, especially ship building. and the automotive industry. The name comes from the V-shaped notch made by a rotating screw at the top of the spindle. The rotation is transmitted to two wheels that are driven by a belt, making them unlike most other tapping machines that use gears. This design allows them to be used in all four corners of a circular object and requires minimal skill for operation. Tapping machines come in different sizes, ranging from small models that can handle simple tasks to large ones that can be used for heavy work. They often have a spindle height above the table of up to 1600 mm. The spindle also has a sharp point at the end, so they are ideal when precise tapping is required.
Drilling machines are highly versatile and provide a great choice for tapping in the construction industry. The 2 main types of drilling machines are the hydraulic drilling machine and the electric drilling machine. . The hydraulic drilling machine is the most common type of drilling machine and uses a hydraulic pump to generate power for the drill. The electric drilling machine also uses a hydraulic pump, but generates power from an electric motor instead. The main difference between these two types of machines is that all the components for pneumatic drills are contained in one unit, but electrical drills use many different units. A pneumatic drill is a type of drilling machine that uses compressed air to provide power for the drill. This type of drilling machine can be categorized into two types: standard and high speed. High-speed drills are able to deliver energy at a high rate, so they require less effort from the operator to complete tasks and greater torque than standard
We will now examine the various types of drilling and tapping machinery and their use in different industries. The installation process is straightforward and can be done without any specialized tools. You just need to unscrew a few screws, change the bit, fix the chuck, put it on a table or bench that’s at least 2 feet high or higher, then tighten the stand so it doesn’t slip off. Since drilling machines are portable and do not require much maintenance, they are highly versatile for tapping as well.
Drilling cum Tapping machines are highly versatile for tapping. The drilling and tapping can be done in a single setup. It is widely used in the field of metalworking, construction, shipbuilding etc. .A tapping machine consists of a spindle and head which are driven by an electric motor. The spindle is mounted on a chuck, which can be rotated in any direction. To set the drill bit to a particular location on the work piece, the chuck is rotated until it has reached the required angle, after which it is locked in place by means of anti
The drilling and tapping can be done in a single setup which is either the table top or floor standing models which are easy to use and highly versatile for tapping. This type of machine is mainly used to drill or tap holes with diameters of 4 mm to 100 mm or more using different types of drills including flat drills, thread drills, end mills etc. .The cutting tools are attached to a rotary table which is driven by a motor and controlled by an electronic controller. Threading drills can be made using the latest technology to have very accurate machining. . The cutting tool is attached to a spindle which is fed by the motor and electronically controlled. These machines are used for machining, milling, turning and other metalworking processes. They are also used in the manufacture of power transmission shafts, bearings etc.
Lastest Articles
-
Embracing NC Hydraulic Press Brake Technology in Middle East Factories
Being a prominent center for indust... -
What machines are used to set up an Electrical Modular Box Plant
Attention all aspiring entrepreneur... -
Manual Process For Making Steel Almirah
Steel almirah are not only durable ... -
Semi Automatic Almirah Making Machines
Streamlining Production Processes w... -
Steel Almirah Manufacturing With Fully Automatic High Precision Machines
Welcome to the world of precision a... -
Unlocking the Power of Precision Understanding the Purpose and Functionality of Drilling Machines
A drilling machine is a tool used f... -
A Beginners Guide to C-Frame Presses for Industrial Applications
Welcome to the world of C-frame pre... -
Busbar Machine Applications in Automotive Manufacturing
Busbar Machine Applications i... -
How Busbar Machines Contribute to Electrical Safety and Reliability
How Busbar Machines Contribute to E... -
A Beginner's Guide to Busbar Fabrication and Assembly
A Beginner's Guide to Busbar Fabric...